PVC CPVC Soild Extrusion Pipe
Cost Saving Solutions
1. Direct Addition - CaCO3
2. Wall control units (scanners)
3. Automatic Thermal Centering (ATC)
4. Gravimetric systems (RGS)
SUPX Direct Addition - RDA
The RDA makes sure that the addition of material to the pvc powder will be done in an exact and consistent way. The RDA unit is mounted on the extruder for constant dosing of hard to handle materials in an industrial environment. High amounts of CaCO3 can be added without the problem of segregation.Multiple dosing units for additives can be mounted providing optimal flexibility for production.
Advantages of RDA systems
• No segregation of CaCO3 and PVC during transport.
• Smoother pipe.
• Blending energy savings.
• Increased flexibility of extrusion line (basis formulation).
• Gravimetric addition of additives.
• High outputs at low reject rates.
Wall Control Units - Scanners
Controlling the dimensions of the pipe during production is an important factor to keep the pipe in the preferred specifications.scanners are able to measure the pipe wall thickness and diameter. A range of scanners with various features is available,covering pipe sizes from 10-1600 mm (1/2” - 60”) diameter.
Advantages of our Scanners:
• Continuous inline wall thickness and diameter measurement
• Minimum wall thickness control (overweight reduction)
Automatic Thermal Centering - ATC
ATC makes it possible to control the distribution of the wall thickness. The ATC can adjust differences in the wall thickness and thus reduce production line start-up time,overweight of the pipe and material scrap.
Gravimetric System - RGS
The core part of the RGS is the weighing hopper. After being filled,the material flows from the weighing hopper into the extruder.The loss in weight per unit of time is equal to the material intake of the extruder. The obtained extruder output is compared to a set reference value and a control system will adjust the extruder screw speed (or dosing speed) to bring the output to the desired level. This control keeps the extruder output stable in spite of fluctuations in bulk density of the raw material.
Instead of the output control, the output signal can also be used for control of the haul-off speed. In that case the pipe weight per meter is kept at a constant level. When the line incorporates an ultrasonic scanner, the measured output is used for automatic calibration of the ultrasonic measurement. This eliminates time consumpting manual calibration procedures.
Process Control System - PCS II
The PCS II itself is a control system that can be combined with a scanner, ATC, RDA, and RGS. The type of scanner, ATC and gravimetric system depends on the extrusion line.
Advantages of our cost saving solutions
• Excellent return on investment
• Reduction of start -up time and scrap
• User friendly interface for total extrusion line control
• Overweight reduction
• Can be used on existing equipment.
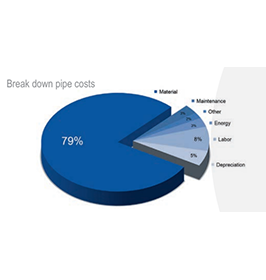
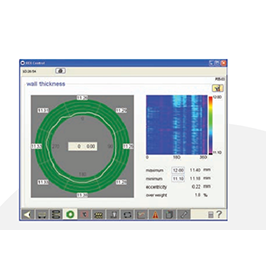
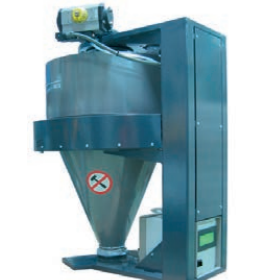